ASME Vessel Heat Transfer Surfaces: Characteristics and Uses
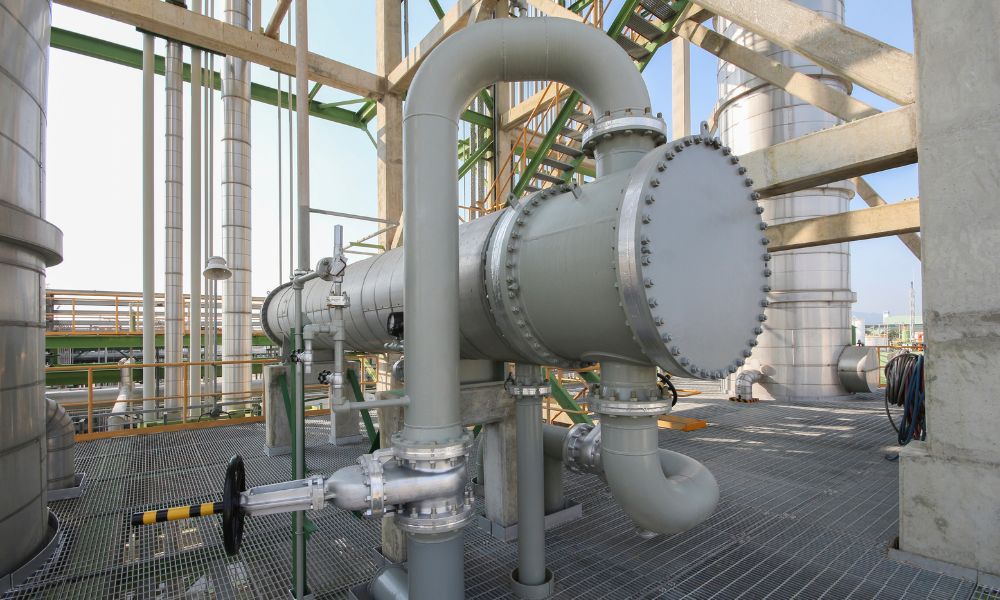
Heat transfer surfaces are pivotal to industrial operations. They are the central nervous system of various processes, from power generation to food and beverage production. Our blog aims to simplify a complex topic to provide a broader understanding; get ready to dive into the characteristics and uses of ASME vessel heat transfer surfaces.
The Characteristics of ASME Vessel Heat Transfer Surfaces
ASME vessel heat transfer surfaces are vital across various industries, including food, pharmaceutical, energy, and bioprocessing. They facilitate efficient heat transfer or cooling in multiple vessel shapes and sizes, demonstrating their adaptability to diverse applications. Read on to explore the characteristics of these surfaces further.
Design Variety
ASME vessel heat transfer surfaces are capable of meeting diverse application needs. The primary external jackets for heat transfer surfaces include conventional, half-pipe, and dimple jackets. The unique advantages of each design make these heat transfer surfaces suitable for multiple applications.
Efficiency
One of the aspects of an ASME vessel heat transfer surface is high efficiency. These surfaces facilitate maximum contact between the thermal fluid and the vessel, leading to efficient heat transfer. This efficiency is vital in maintaining temperature control, which supports the quality of the vessel’s contents.
Durability and Robustness
ASME vessel heat transfer surfaces are known for their durability and robustness. These surfaces ensure that the industrial processes are problem-free while extending operational lifespan. The durability of the surfaces improves high-pressure fluid handling, particularly in designs such as the half-pipe jacketed vessel.
Versatility
ASME vessel heat transfer surfaces exhibit great versatility, finding use in numerous industries such as food, pharmaceutical, energy, and bioprocessing. They are pivotal in processes such as pasteurization, sterilization, and energy recovery.
Materials Commonly Used in Heat Transfer Surface Construction
The construction of ASME vessel heat transfer surfaces requires meticulous attention to detail, particularly concerning material selection.
Stainless Steel
Stainless steel is a widely used material in the construction of heat transfer surfaces. This material is popular because of its excellent properties, such as remarkable heat transfer and efficient exchange of thermal energy. This material also has high corrosion resistance, making it ideal for use in applications where it may encounter corrosive fluids or environments.
Copper
Copper is another metal used in heat transfer surfaces. It is popular for its superior thermal conductivity, facilitating rapid and efficient heat transfer. Copper is an excellent choice for applications that need high-speed heating or cooling. However, copper corrodes quickly, so it is not suitable for all tasks.
Aluminum
Aluminum is a lightweight material with more uses than copper; though its conductivity is lower than copper, it’s still higher than other materials. Aluminum’s combined qualities ensure it remains suitable for heat transfer applications.
Extensive Application of Heat Transfer Surfaces Across Major Industries
ASME vessel heat transfer surfaces have extensive use in various industries. These surfaces are fundamental to many industrial processes where precise temperature control and efficient energy utilization are key.
Pharmaceutical Industry
The pharmaceutical sector requires a set temperature in their vessels to ensure the contents don’t go bad. Pharmaceuticals use reactors and fermenters to facilitate controlled heating or cooling. The equipment helps maintain the required temperature conditions, which are vital during the synthesis of active pharmaceutical ingredients (APIs) and biotechnological processes such as fermentation.
Food and Beverage Industry
The food and beverage industry relies heavily on ASME vessel heat transfer surfaces. These surfaces are necessary for pasteurization, sterilization, brewing, and distillation. These surfaces allow for more precise temperature control, which is crucial in industries where taste, texture, and product safety directly impact consumer satisfaction.
Power Generation Industry
The power generation industry is another key sector where heat transfer surfaces are beneficial. In this industry, energy efficiency and environmental impact are important. Power generation factories use ASME vessel heat transfer surfaces for their boilers, condensers, and heat exchangers. These shells enhance energy efficiency, reducing heat waste and diminishing the environmental footprint.
Chemical Industry
The chemical industry utilizes vessel casements to maintain a temperature-set range for optimal efficiency and safety. They are most beneficial in reactors, distillation columns, and heat exchangers, ensuring process efficiency and safety.
Oil and Gas Industry
ASME heat transfer vessel surfaces improve refining, distillation, and reformation so that professionals can meet specific temperature conditions. This precise temperature control is crucial for transforming natural oil into usable products such as gasoline, diesel, and jet fuel.
Dairy Industry
The dairy industry also relies on ASME vessel heat transfer surfaces. These surfaces are fundamental for pasteurization, homogenization, and sterilization processes. ASME vessel shells have exact temperature control, which helps professionals achieve the required safety standards of the products—meeting these product safety standards impacts consumer health and satisfaction.
Textile Industry
The textile industry utilizes ASME vessel heat transfer surfaces in dyeing, drying, and heat setting. Precise temperature control in these processes improves the finished product’s quality. Heat transfer surfaces help maintain the product’s color vibrancy and structural integrity.
Pulp and Paper Industry
Heat transfer surfaces help with pulp cooking, bleaching, and paper drying processes in the pulp and paper industry. These surfaces optimize energy usage and improve process efficiency. These factors are critical for creating sustainable and profitable industry operations.
Aerospace Industry
The aerospace industry employs heat transfer surfaces in aircraft and spacecraft design. These surfaces aid in managing the heat generated during flight, ensuring the safety and performance of these vehicles.
Dimple Jacket Welding: Enhancing Efficiency in Heat Transfer
While learning about ASME heat transfer surfaces and their characteristics and uses, let’s pause and look at an essential technique: dimple jacket welding. This technique designs a dimple jacket pattern on the heat transfer shell, increasing heat exchange and improving efficiency. Dimple jacket welding requires precision and expertise, meaning that it’s best to partner with experienced fabricators when constructing heat transfer surfaces.
Come To CMPI For Heat Transfer Services
Many industries can utilize ASME vessel heat transfer surfaces to improve everything from product quality to energy efficiency. Understanding their design principles, geometries, and construction materials can help businesses make informed decisions and optimize operations.
Strive for better energy efficiency and benefit your products and customers by hiring Custom Manufacturing and Polishing Inc. to design ASME heat transfer surfaces for your vessels. Our team strives to create unique designs using industry-standard practices. When working with us, you can create your heat transfer shells with dimple jacket welding , a practice that increases heat exchange throughout the vessel. Contact us for information on our welding services.
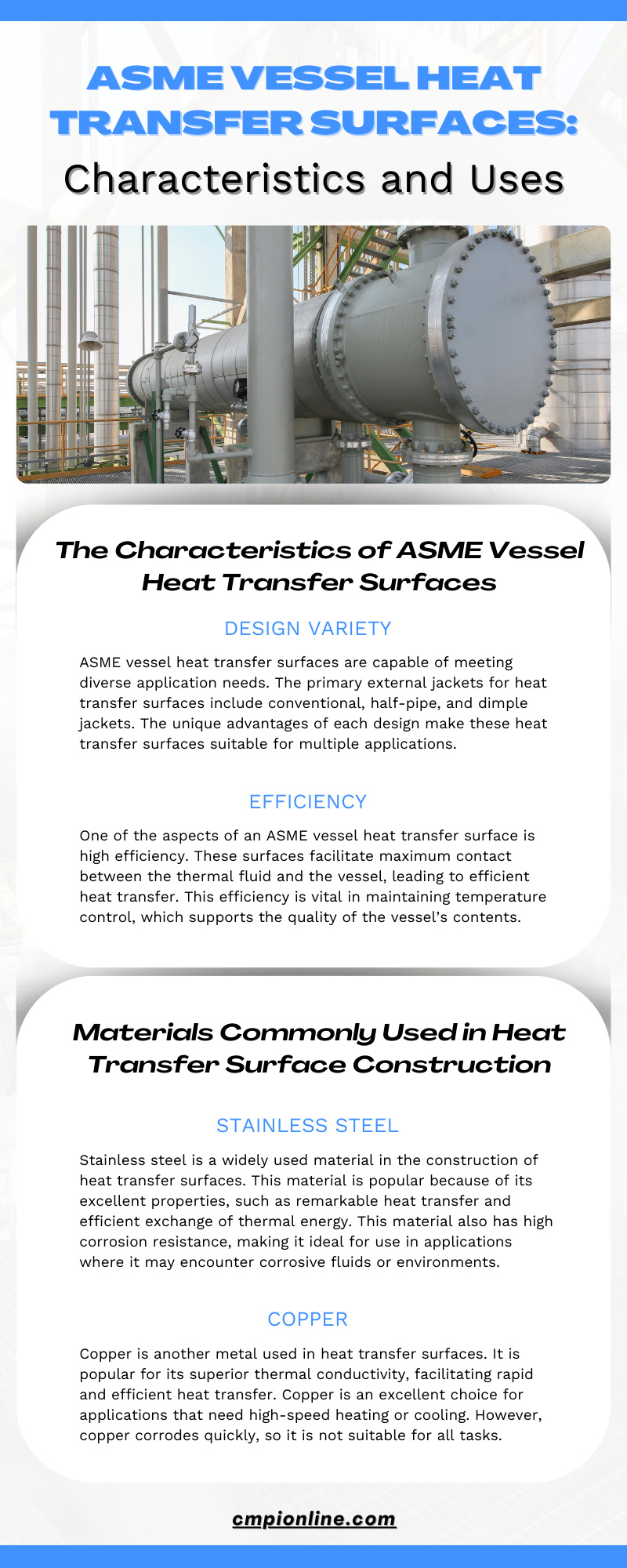