Dimple Jackets vs. Conventional Heat Transfer Methods
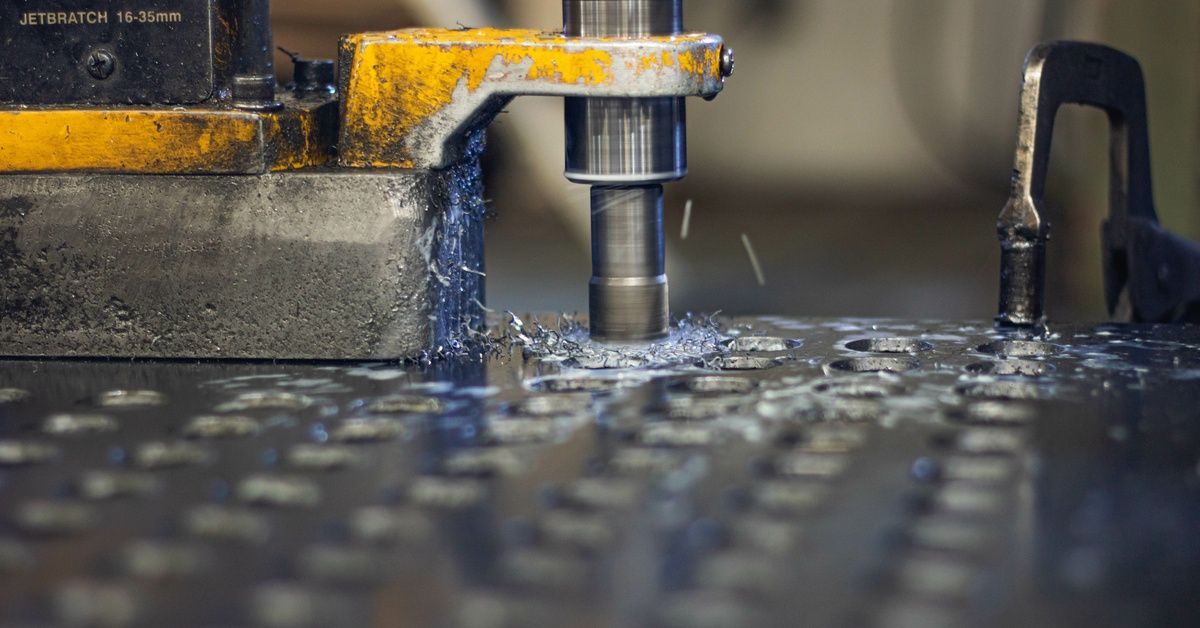
When designing tanks, vessels, or reactors that require precise temperature control, manufacturers often face a key decision: what type of heat transfer system to use. The debate between dimple jackets and conventional heat transfer methods continues to shape how industries approach thermal management in stainless-steel fabrication. While both approaches offer distinct advantages, dimple jackets are increasingly becoming the preferred solution for a wide range of applications.
What Are Dimple Jackets?
Dimple jackets are thin sheets of metal, typically stainless steel, spot-welded to the surface of a vessel to form a pattern of dimples. This structure creates an internal flow path for heating or cooling media. The design promotes efficient thermal exchange while minimizing material usage and overall tank weight.
Conventional Heat Transfer Methods
In contrast, conventional methods, such as full-jacketed vessels or internal coils, rely on bulkier designs. Full jackets wrap the entire vessel with a second wall, creating a chamber for heating or cooling fluids. Internal coils, meanwhile, sit inside the vessel and transfer heat directly into the contents. These setups are effective but come with drawbacks such as reduced usable volume, higher material costs, and more complex maintenance.
Key Benefits of Dimple Jackets
The efficiency of dimple jackets lies in their simplicity. Because they use less metal than traditional jackets, they reduce overall fabrication lead times. Additionally, the design promotes even heat distribution, thereby minimizing the risk of hot spots or temperature gradients within the vessel.
Dimple jackets are typically more cost-effective to produce and install. Their lightweight design reduces material costs and simplifies handling. They’re also customizable, ensuring optimal heat transfer for diverse industrial needs. Lastly, their structural integrity makes them highly resistant to pressure fluctuations.
Comparing Performance
When comparing dimple jackets and conventional heat transfer methods, dimple jackets often outperform in categories like cost efficiency and compactness. Conventional jackets, however, may still be suitable for certain high-volume or high-temperature applications where the design allows for more surface area or fluid volume within the jacket.
That said, dimple jackets generally require less maintenance. With no internal components to clean and fewer welds to inspect, they’re easier to sanitize and maintain over time, a major consideration in industries with strict hygiene regulations.
Choosing the Right Partner
Ultimately, the right choice comes down to your specific application, process needs, and design constraints. Whether you’re building a custom tank or upgrading existing equipment, working with an experienced dimple jacket manufacturer ensures you can depend on your system for performance, safety, and long-term reliability.
For precision fabrication and polished stainless-steel solutions, call CMPI. We have the expertise to deliver vessels that meet demanding thermal requirements across various industries.