How To Choose the Right Sheet Metal for Your Project
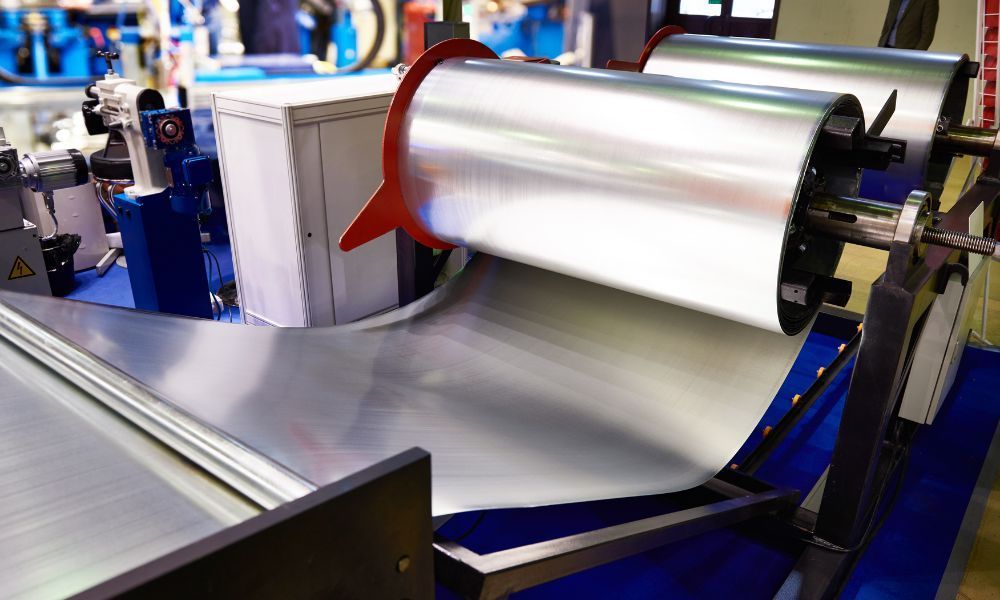
Metal manufacturing is the industry to look into for opinions on what sheet metal is right for your project. You can ask your co-workers, or you can rely on the expertise of a professional metal fabrication shop. Whatever path you decide to follow, make sure you’re getting the best advice for your project. Read on to learn more about how to choose the right sheet metal for your project.
Why Do You Need a Guide on Choosing Sheet Metal?
Having a guide prompts a reader to ask questions before they start their project and understand the essential things they need to look for in sheet metal. The following list helps you understand the basics of what you need to consider in sheet metal, such as tensile strength and machinability. These things help you find what you’re looking for without spending too much time comparing one type of alloy to another.
The Key Factors of Picking Sheet Metal
Here’s the thing: you won’t be able to pick a good metal type without knowing how well it works in different environments or if it welds well. Instead of going with your heart, learn the essential factors for choosing sheet metal.
Ductility and Formability
Ductility makes a metal easy to form into a wire or other smaller, intricate parts. Without ductility, there is no way for metal to break down as quickly. The other part of picking a metal is determining if it is formable—if it isn’t, the metal can’t form into a different shape or bend without snapping.
Tensile Strength
Tensile strength stems from formability, which is a word used to describe a metal’s strength. If it has a low strength, it won’t be able to bend in specific ways without falling apart. If a project requires significant force, this is the one factor to pin at the top of your most desired list for metals.
Machinability
Machinability describes how well a metal can cut on a blade. If you choose a tougher alloy type, you’ll need special tools to cut through so you can process it through a machine. Keep the types of machines you currently have with you in mind when picking a material for your project.
Weldability
A company looking for metals to weld with needs to pay attention to this section—a metal’s weldability depends on its cooling rate, electrode material, welding speed, and shield gases. In this case, it’s best to steer clear of carbon and certain stainless steel types, as they may take longer to weld.
Questions To Ask Yourself When Selecting Sheet Metal
Start preparing your answers to these fundamental questions now as you prepare to talk with a professional metal fabrication shop.
What Grade and Thickness Do You Need?
If you need a thick metal type, it’s essential to look for this when picking a metal—selecting something that is too thin delays your project, leading to unaffordable costs. Avoid spending more money than necessary by learning the thickness difference between metal foils, plates, and sheets before buying.
What Project Are You Working On?
Ensuring the project you’re working on requires metal sheets is essential. You can’t just pick a metal and not know if the project requires it. Look over your project’s details to learn what materials you need the most. If the metal type needs a specific tensile strength or durability level, it’s essential to look for those characteristics in metal sheets.
Does the Metal Need Corrosion Resistance?
Know the corrosion resistance of metal alloys before picking—knowing this information spares you from facing consistent maintenance problems. Checking corrosion resistance is the best way to ensure your maintenance workers don’t spend too much time wiping away rust because you didn’t realize the material had low degradation resistance.
Do You Want Design and Finishing Options?
Design and finishing aren’t a requirement, but knowing you have the option to design something unique for a building or other project is essential. Most contractors looking into how to choose a metal type for their project may overlook this because it seems unnecessary, but it actually could make a structure stand out. If you have a moment to discuss design and finishing options with a metal fabricator, listen to what they say.
Overview of Sheet Metal Materials
Now that you have explored essential questions about your project, let’s look at sheet metal alloys that might work for you.
Stainless Steel
Stainless steel (SS) is a great material because it’s durable, highly hygienic, and eco-friendly. SS has many grades, including the popular austenitic SS series 300—which is magnetic; the others, ferritic and martensitic, are non-magnetic. However, this material is pricey and can still show signs of rust.
Copper
Copper is a beautiful decorative metal that is inexpensive and completely malleable. It’s easy to form this metal into any shape you’d like. However, one drawback of copper is that it’s an electrical conductor. If the wire ever frays, it could cause an electrical current leading to power outages and fires.
Aluminum
Aluminum is a fantastic choice if you need an affordable alloy with characteristics similar to stainless steel—both are corrosion-resistant and form into any shape or size you desire. The biggest downside is that it’s vulnerable to high temperatures, so if you are in a warmer climate, it’s a good idea not to use aluminum.
Overview of Sheet Metal Fabrication Processes
The last thing to go over is the metal fabrication processes. While working with a metal fabricator, they’re going to mention different procedures to use on metal sheets. During the conversation, you will learn about the pros and cons, a brief description of the process, and what metals are best for these processes.
Cutting
The procedure uses a blade to shear the metal. The processes include photochemical machining, a CAD system that draws a cut out using a stencil, and laser cutting, which uses a chemical mixture to cut clean edges.
Bending
A bending machine grabs onto a metal sheet and uses geometry stamps to press metals into different shapes. This process generally uses a punch and stamp method that bends the metal at or above 90-degree angles to achieve a shape.
Hemming
If you need a tight fit or edge, hemming is the method. The hemming process folds its edges, creating a tighter hold around itself or another metal piece. Your metal fabricator can discuss this process more, including the differences between the two hemming processes: roll hemming and conventional die. The main difference is that roll hemming uses a roller, while conventional die uses a hemming tool to fold the metal.
Custom Manufacturing and Polishing, Inc doesn’t gatekeep. We enjoy helping customers like yourself understand the difference between copper and stainless steel sheet plates. We’re just as curious as you to learn more about your project so that we can recommend the best service. Our team of highly-trained metal fabricators is here to bring your creation to life and walk you through the right metal for your project.
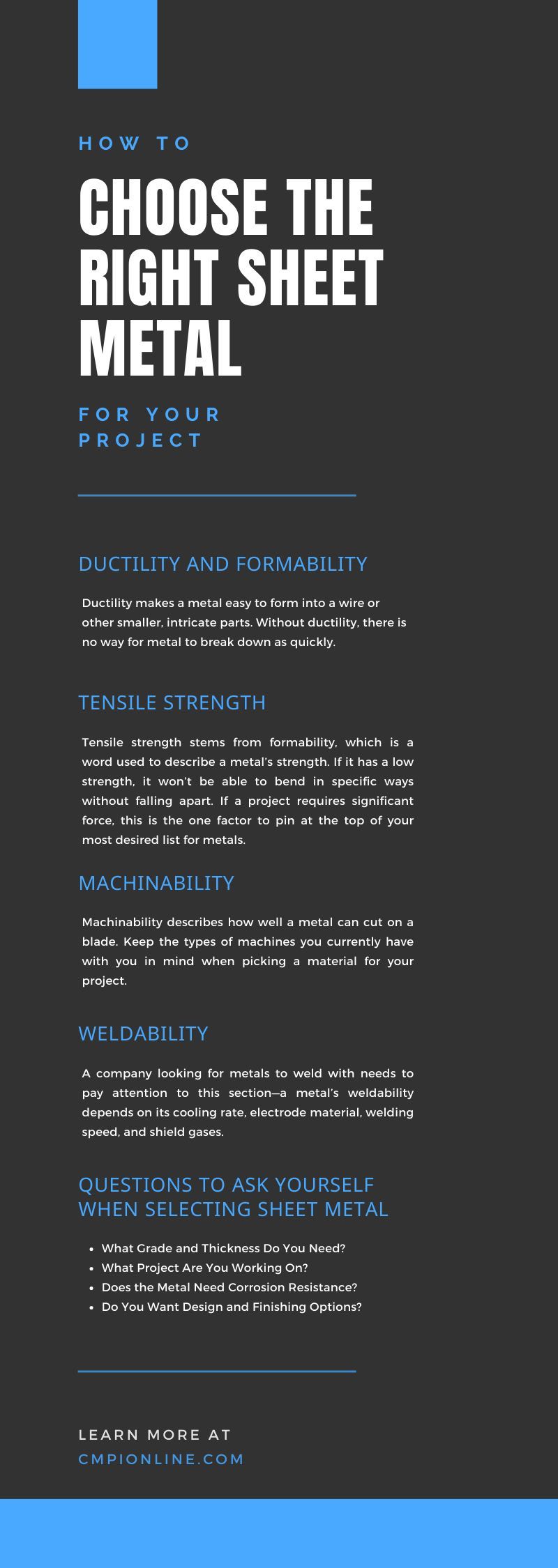