The Evolution of Stainless Steel Fabrication Techniques
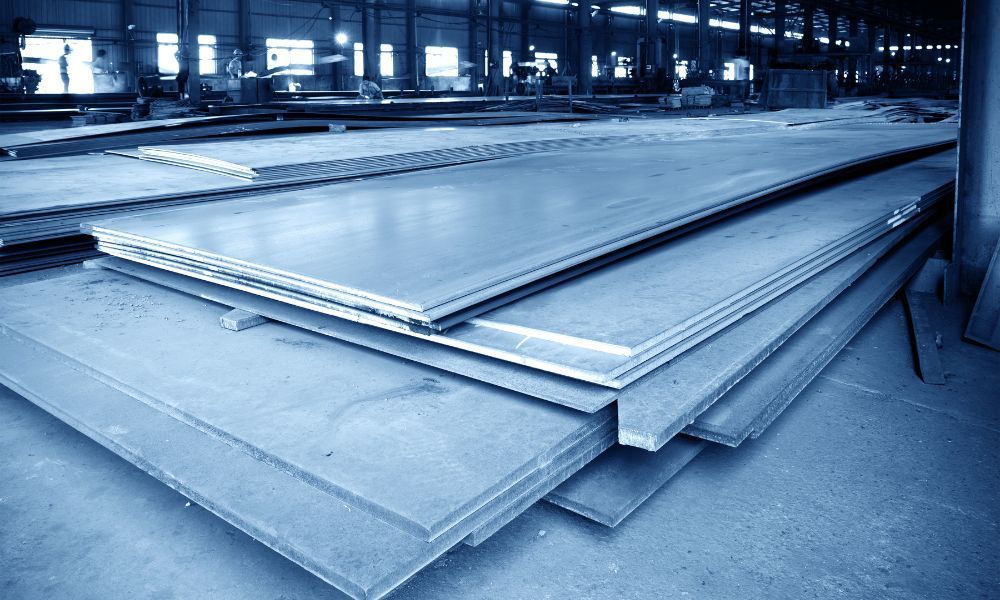
Metal fabrication is an art form that has continuously shaped the world around us, transitioning from manual labor to precision-driven engineering. This transformation is especially evident in the fabrication of stainless steel, a material renowned for its durability, corrosion resistance, and sleek appearance. Let’s explore the evolution of stainless steel fabrication techniques by examining the historical use of this alloy, traditional production methods, and emerging trends.
Historical Background
The history of stainless steel is a testament to human ingenuity, with roots that date back to the early twentieth century. It was an era dominated by the need for material sciences to catch up with the rapid industrial expansion. In 1913, British metallurgist Harry Brearley created the first true stainless steel, which was initially intended for cutlery, surgical instruments, and high-stress applications due to its resistance to oxidation and corrosion. This innovation sparked a revolution, altering the technological landscape across multiple industries.
Given its unique properties, stainless steel swiftly found its way into various manufacturing sectors. In the 1920s, power stations and underground stations used stainless steel due to its resistance to high-temperature steam and corrosive environments. By the 1930s, stainless steel began its ascent in construction, with landmarks like the Chrysler Building featuring the gleaming metal. Its use in food processing, pharmaceuticals, and automotive manufacturing during the mid-twentieth century solidified stainless steel as an essential building block of industry.
Traditional Fabrication Techniques
Before the dawn of sophisticated machinery, crafting stainless steel required time-honored techniques that relied on the skill of the fabricator and the precision of their tools. Forming stainless steel involved hammering heated bars into shape, a method known as forging, or precision bending and forming using mechanical presses. Cutting stainless steel was a slow, labor-intensive process, often involving shearing, sawing, or hand-held torches.
The early days of stainless steel fabrication were a time of manual labor and craftsmanship. Stainless steel, although advantageous in its physical properties, was difficult to work with, especially when trying to attain the smooth, seamless finishes characteristic of the material. Fabricators relied on their experience to shape the metal, often taking days to create a single component. Precision was key, and any mistake during the process could result in an irreparable flaw—a stark contrast to the near-infallible processes found in modern fabrication.
Evolution of Techniques
Some pivotal moments in the stainless steel fabrication industry came with the introduction of new technologies that revolutionized the precision and efficiency of the process. These advancements met the growing demand for stainless steel across consumer and industrial products. Laser cutting technology emerged as an efficient way to cut stainless steel and other metals with a high level of accuracy, leaving behind a smooth edge that required minimal post-processing.
Computer numerical control (CNC) machining systems provided a level of precision previously unattainable, automating much of the fabrication process and allowing for complex designs with tight tolerances. Perhaps the most transformational was the advent of 3D printing, which introduced a layer-by-layer fabrication method capable of producing intricate stainless steel components with minimal waste and unprecedented design freedom.
Industrial Impact
The implementation of these new techniques has had a profound impact on the stainless steel fabrication industry. Laser cutting and CNC machining significantly reduce lead times, allowing for faster order fulfillment and prototyping. The precision and repeatability of these processes means that component assembly is more streamlined, reducing the margin of error and the need for manual correction. 3D printing’s entrance into the fold marked a turning point in design complexity, manufacturing agility, and material efficiency, addressing unique needs with unprecedented ease.
The efficiency and precision offered by modern fabrication techniques like laser cutting and CNC machining are unmatched. With reduced manual intervention, the risk of errors drastically decreases, resulting in components that meet the most stringent quality standards.
Additionally, an often-overlooked aspect of the evolution of fabrication techniques is the impact on worker safety. Traditional fabrication methods, which often involved handling heavy materials and working close to intense heat sources, were hazardous. The transition to more automated and controlled processes with minimal human interaction has led to safer working environments. Safety protocols combined with the precision of modern machinery have significantly reduced the possibility of workplace accidents.
Future Trends
The stainless steel industry stands on the edge of a technological precipice, with emerging trends poised to redefine what we previously deemed too complex or costly. One of these trends is the rise of smart fabrication, integrating sensors and data feedback to refine the production processes.
The industry also anticipates further advancements in 3D printing, such as the capacity to print larger components at faster rates, opening doors to industrial-scale applications and allowing for on-demand production. Additionally, the intersection of artificial intelligence (AI) with machine tool technology holds the promise of autonomous manufacturing, creating a system where machines can learn and adapt to optimize their fabrication efficiency.
Smart Fabrication
Smart fabrication takes the principles of automation and adds a layer of insight. By equipping fabrication machinery with sensors that collect data throughout the production process, fabricators can gain a deeper understanding of material behavior, machine performance, and product quality. This information can adjust parameters in real time, ensuring optimal production runs with minimal waste or rework.
Advancements in 3D Printing
The potential for 3D printing to revolutionize the fabrication of stainless steel components is only beginning to be realized. Innovations in printing technology, such as new metal alloys printed at room temperature, are expanding the range of applications and materials. Future progress in this area will undoubtedly result in stronger, more resilient structures that could challenge the existing limitations of stainless steel fabrication.
Autonomous Manufacturing
The integration of AI in fabrication holds the key to autonomous manufacturing, where machines make decisions and adjustments without human intervention. This self-optimizing system could significantly increase efficiency and potentially open new avenues for stainless steel production. Autonomous fabrication, built on a foundation of AI and robust data analysis, would usher in a new era of production, where design and physical component are seamlessly integrated.
A Spirit of Innovation
The evolution of stainless steel fabrication techniques is constant. By continually adapting, fabricators can leverage the strengths of emerging trends, honor the past, and shape a future where stainless steel is at the forefront of human achievement. Metal fabrication is an ever-present testament to the indomitable spirit of innovation and progress.
CMPI is a stainless steel fabrication service with a knack for all things metal. We can help you polish and finish your stainless materials to your exact specifications. Contact us today to learn more about our custom stainless steel polishing and fabrication services.
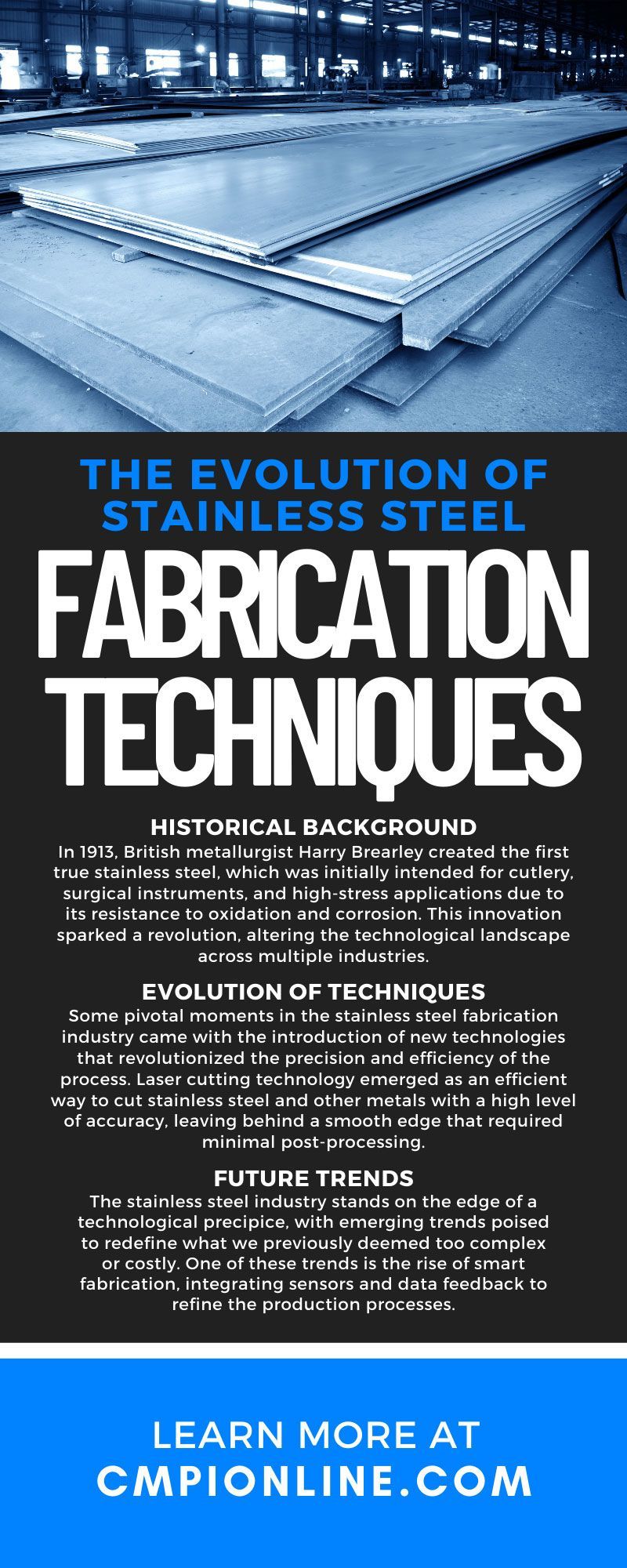