The Role of Thermal Conductivity in Stainless Steel
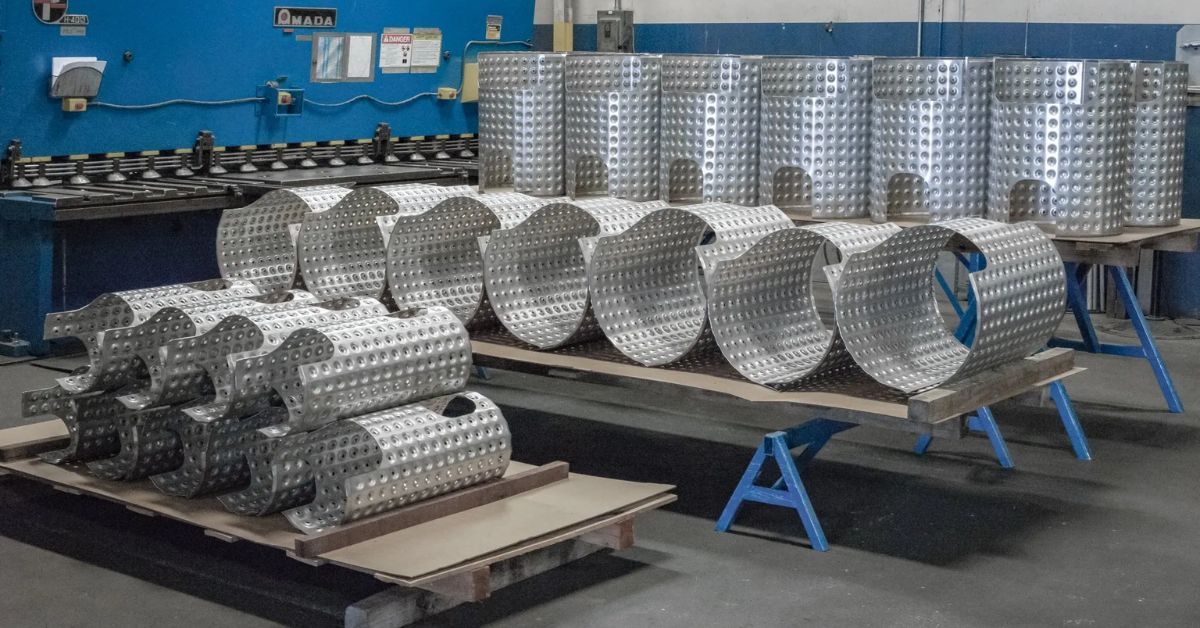
Stainless steel is a versatile material used across industries, from architecture to food processing to manufacturing. One of its lesser-known but crucial properties is its thermal conductivity. While its resistance to corrosion and strength often steal the spotlight, thermal conductivity plays a role in stainless steel’s performance in various applications, particularly in heat transfer systems.
What Is Thermal Conductivity?
Thermal conductivity measures how well a material can conduct heat. Materials with high thermal conductivity, such as copper and aluminum, transfer heat efficiently, while materials with low thermal conductivity retain heat for longer periods.
Stainless steel falls into the latter category. In fact, stainless steel has relatively low thermal conductivity compared to other metals, placing it in a unique position for some applications. Its low heat transfer rate allows for controlled heating and cooling, making it ideal for precision tasks.
Factors Affecting Stainless Steel’s Thermal Conductivity
Several factors influence stainless steel’s thermal conductivity. By understanding these variables, manufacturers and engineers can optimize designs to balance heat transfer efficiency and durability.
Alloy Composition
Stainless steel isn’t a single material but a family of alloys. Common grades like 304 and 316 differ in composition, leading to variations in thermal conductivity. For example, 304 stainless steel has a slightly lower thermal conductivity than 316, making the latter a better choice for heat-intensive applications.
Temperature
Thermal conductivity can also vary with temperature. Stainless steel becomes more conductive at higher temperatures, an important consideration when designing for industries like food processing or chemical manufacturing.
Material Thickness and Finish
Thicker sheets of stainless steel tend to have lower thermal conductivity because the heat takes longer to transfer through the material. Surface finish also plays a role, as polished or treated surfaces can impact the material’s ability to transfer heat efficiently.
How Thermal Conductivity Impacts Heat Transfer Systems
The value of thermal conductivity in stainless steel is clear when considering heat transfer systems. Understanding and optimizing this property allows the use of equipment such as heat exchangers, tanks, and dimple-jacketed reactors.
Heat transfer systems work by transferring energy from one point to another. In most cases, the objective is to heat or cool a substance in a contained space. Thermal conductivity is particularly important in this process because it affects the heat transfer rate through the material.
The role of thermal conductivity in stainless steel heat transfer systems becomes even more pronounced when considering industrial applications. Maintaining precise temperature control is crucial for efficient and safe operations in many industries, including chemical processing and food production. Understanding the thermal conductivity of the different materials in these processes allows for equipment that maximizes heat transfer efficiency and minimizes energy loss.
Heat Exchangers
Heat exchangers use stainless steel due to its durability and corrosion resistance, even in extreme temperature environments. The low thermal conductivity ensures gradual and consistent heat transfer, preventing rapid temperature spikes that can damage equipment or affect product quality.
Food and Beverage Processing Tanks
Controlled heating and cooling are vital during food and beverage production. Stainless steel’s ability to withstand temperature changes while ensuring even heat distribution makes it a preferred material for fermenters, kettles, and holding tanks.
Industrial Manufacturing
Fabrication techniques like welding and forming heavily depend on thermal behavior. With stainless steel, localized heat application prevents unnecessary warping or distortions, ensuring structural integrity.
Cryogenic Applications
Even in extremely cold conditions, stainless steel maintains its properties without becoming brittle. This makes it invaluable in cryogenic systems, where insulation and controlled thermal conductivity are essential.
Architectural Use
Outdoor structures, railings, and claddings often experience temperature extremes. Stainless steel’s ability to resist expansion or contraction from temperature fluctuations ensures long-lasting performance with minimal maintenance.
Dimple Jacketed Reactors
Stainless steel’s thermal conductivity and corrosion resistance make it a popular choice for dimple-jacketed reactors, which are common in industries such as pharmaceuticals, food and beverage, and chemical processing. Dimple jacket welding creates a design on the tank’s exterior that maximizes efficiency in heat transfer between heating or cooling fluids and the inner vessel, ensuring precise temperature control during production.
Benefits of Stainless Steel’s Low Thermal Conductivity
While some manufacturers may see low thermal conductivity as a drawback compared to materials like copper or aluminum, it offers several unique advantages.
Improved Safety
Stainless steel allows for more uniform heat transfer, reducing the risk of sudden hot spots that could damage equipment or endanger operators. Additionally, its high melting point makes it a safer choice for handling potentially hazardous substances.
Energy Efficiency
Because stainless steel’s low thermal conductivity maintains temperature stability, less energy is required to heat or cool substances during production. This can result in significant cost savings over time.
Durability and Corrosion Resistance
Unlike highly conductive materials like copper, stainless steel offers exceptional resistance to corrosion, even in environments where certain chemicals or moisture are present. This is valuable in many scenarios.
Maintenance of Thermal Stability
Slow, controlled heat transfer is ideal for many industrial applications. Stainless steel’s thermal properties reduce rapid temperature changes that can compromise product consistency.
Maximizing Thermal Performance in Stainless Applications
Making the most of stainless steel’s thermal conductivity requires the right tools and expertise. Businesses can optimize thermal performance across various applications by selecting the appropriate stainless-steel grade and partnering with a company that employs advanced fabrication techniques.
Here are tips for you or your fabricators:
- Use waterjet cutting or laser welding to reduce unwanted heat-affected zones.
- Consider using stainless steel with higher nickel content for applications requiring high thermal conductivity.
- Explore hybrid materials, such as aluminum-clad stainless steel, for enhanced thermal performance and weight reduction.
- Incorporate design features such as fins or channels to increase the surface area available for heat transfer.
The CMPI Difference
When it comes to leveraging stainless steel’s unique properties, expertise matters. At CMPI, we specialize in custom stainless-steel solutions tailored to your specifications. Our services include cutting-edge fabrication techniques, as well as the following:
- polishing to enhance surface performance and aesthetics
- welding, including ASME- and AWS-certified processes
- heat transfer solutions, such as dimple jacket manufacturing
If your project requires balancing durability, precision, and efficiency, CMPI delivers dependable stainless-steel solutions that shine in performance. Contact us today, or request a quote to get started.
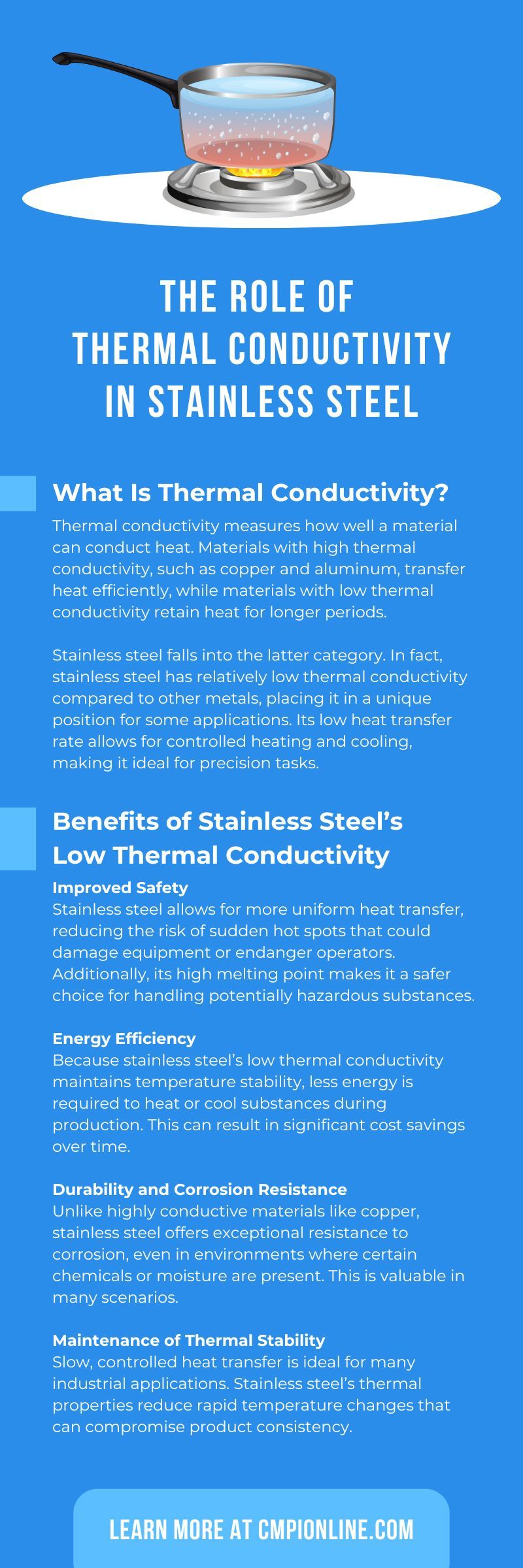