Understanding Heat Transfer Efficiency in Dimple Jackets
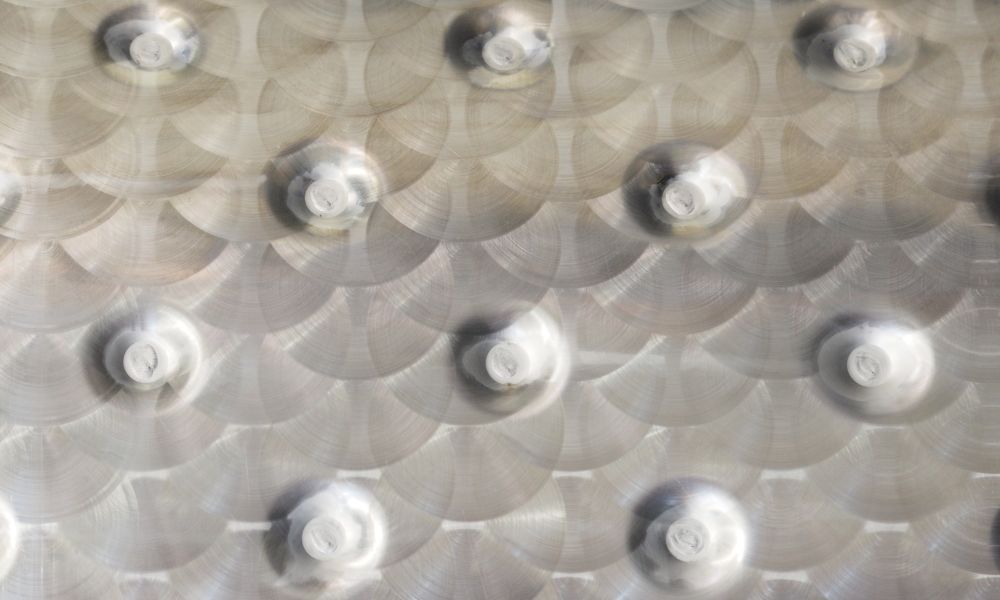
Manufacturing companies must constantly innovate to improve processes where heat transfer efficiency is paramount. One such innovation, known as a dimple jacket, has revolutionized the way we design vessels for heat exchange.
These unique thermal solutions are specifically engineered with an outer layer of dimples or embossed patterns. The addition of a secondary channel optimizes manufacturing operations by enhancing heat transfer across these surfaces, making them invaluable for various industries, from chemical processing to brewing. That’s why understanding heat transfer efficiency in dimple jackets is critical. Continue reading to learn why they’re a game-changer for manufacturers.
Increased Surface Area
The secret of a dimple jacket’s effectiveness lies in its geometry. By introducing a dimpled surface to a vessel, you dramatically increase the surface area through which heat is transferred. The larger surface area provides more contact for the heat transfer medium, whether it’s steam, water, or a refrigerant, allowing for efficient heat transfer. This means more products can be heated or cooled in a shorter time, which is an enormous asset in high-volume manufacturing.
Surface area, in its various geometrical forms, dictates the efficiency of heat exchangers. Dimple jackets offer a finely tuned balance between increasing surface area and maintaining structural integrity. When compared to flat surfaces, dimpled ones can enhance the heat transfer rate significantly.
Enhanced Turbulence
Turbulence in heat transfer systems acts as an efficient disruptor. With dimple jacket systems, the process fluid gets whipped around in the dimples, breaking up laminar flow and converting it into a more chaotic, turbulent motion. This turbulence is more effective at transferring heat, as it brings colder or hotter fluid into direct contact with the surface more often, ensuring a thorough exchange.
The heat transfer efficiency of dimple jackets is magnified by the chaotic convections created by the dimples. These convections work to strip away the insulating film that can form on the heat transfer surface, thus maintaining high heat transfer rates. When combined with enhanced surface area, the turbulence facilitated by dimple jackets means heat is exchanged more rapidly, which can be vital for maintaining an optimal process temperature profile.
Improved Heat Transfer Coefficients
Heat transfer coefficients are critical when it comes to heat exchange. High coefficients signal efficient heat transfer, and dimple jackets work wonders in elevating these values. The irregular pattern of the dimples on the vessel’s surface results in altered flow patterns of the heat exchanger’s process fluid. This change in flow encourages greater heat transfer, leading to an increase in the overall heat transfer coefficient.
Enhanced heat transfer coefficients mean dimple jackets enable more effective heat transfer. Manufacturers can benefit from shorter processing times and achieve higher throughput rates. Plus, in processes where maintaining an exact temperature is crucial, a better heat transfer coefficient can provide a more stable and controlled process, reducing the chances of product inconsistencies.
Efficient Cooling and Heating
In the realm of manufacturing, precision is often the difference between a perfect batch and a failed one. Dimple jackets deliver precision through efficient cooling and heating. By maintaining a consistent and controlled heat transfer process, they ensure that products are processed under ideal temperature conditions. High heat transfer efficiency means better temperature control and lower energy consumption, both of which are critical components for cost-effective and environmentally friendly manufacturing.
Reduced Fouling
Fouling is an inevitable opponent in the battle for optimal heat transfer efficiency. It can reduce the surface area available for heat transfer and increase the resistance to flow. Dimple jackets, with their inherent design, help combat fouling. The increased turbulence and enhanced coefficients keep the surface active and discourage the buildup of contaminants.
Reduced fouling prolongs maintenance intervals and minimizes downtime for cleaning, having a direct impact on the profit margins of manufacturing companies. By preventing or delaying fouling, dimple jackets ensure that the heat exchanger works at peak performance for extended periods, contributing to a smoother, more cost-effective operation.
Uniform Temperature Distribution
For certain manufacturing processes, maintaining a uniform temperature throughout the entire vessel is a non-negotiable requirement. Dimple jackets excel at this, distributing the heating or cooling medium evenly across the vessel’s surface, resulting in a balanced temperature profile. Uneven temperature distribution can lead to product inconsistency or even spoilage, making the uniformity provided by dimple jackets a critical advantage.
Manufacturers in the food and beverage, pharmaceutical, and other stringent regulation-dependent industries rely on the uniform heat transfer facilitated by dimple jackets to ensure high-quality products. From preventing hot spots to ensuring every molecule in the product is exposed to the same heat exchange, uniform distribution is a hallmark of the dimple jacket system.
Cost-Effectiveness
The efficacy of heat exchangers is not just about fast and flawless processes. It’s also about the cost. Dimple jackets, with their plethora of heat transfer benefits, contribute to making processes more cost-effective. They decrease process duration, ensure more uniform heating and cooling, and minimize maintenance requirements, resulting in considerable savings in the long run.
The initial cost of integrating dimple-jacketed vessels may be higher, but the return on investment is often swift. With the potential for increased production capacity and reduced energy use, the long-term savings on operational costs can be substantial. Additionally, the ability to prevent product spoilage and maintain high standards can protect a manufacturer’s brand image, which is invaluable.
A Series of Energetic Exchanges
Understanding heat transfer efficiency in dimple jackets means recognizing that manufacturing, at its core, is a series of energetic exchanges. Each involves intricacies of heat transfer, and the battle for efficiency requires tools that wield thermodynamics’ laws to our advantage. Dimple jackets, with their innovative approach to surface design, positively affect heat transfer in novel ways.
From increased surface area to better heat transfer coefficients, dimple jackets check all the boxes for efficient heat exchange. They provide a solid balance of enhanced performance and reduced operational costs, turning them into a necessity for companies that value precision and productivity in their processes.
As a proud dimple jacket manufacturer, CMPI can help you optimize heat transfer by attaching our sheets to the outside of your fabrications. We offer affordable and high-quality dimple plates customized to fit your specific requirements. Browse our large selection and contact us to learn more about our professional fabrication and welding services today!
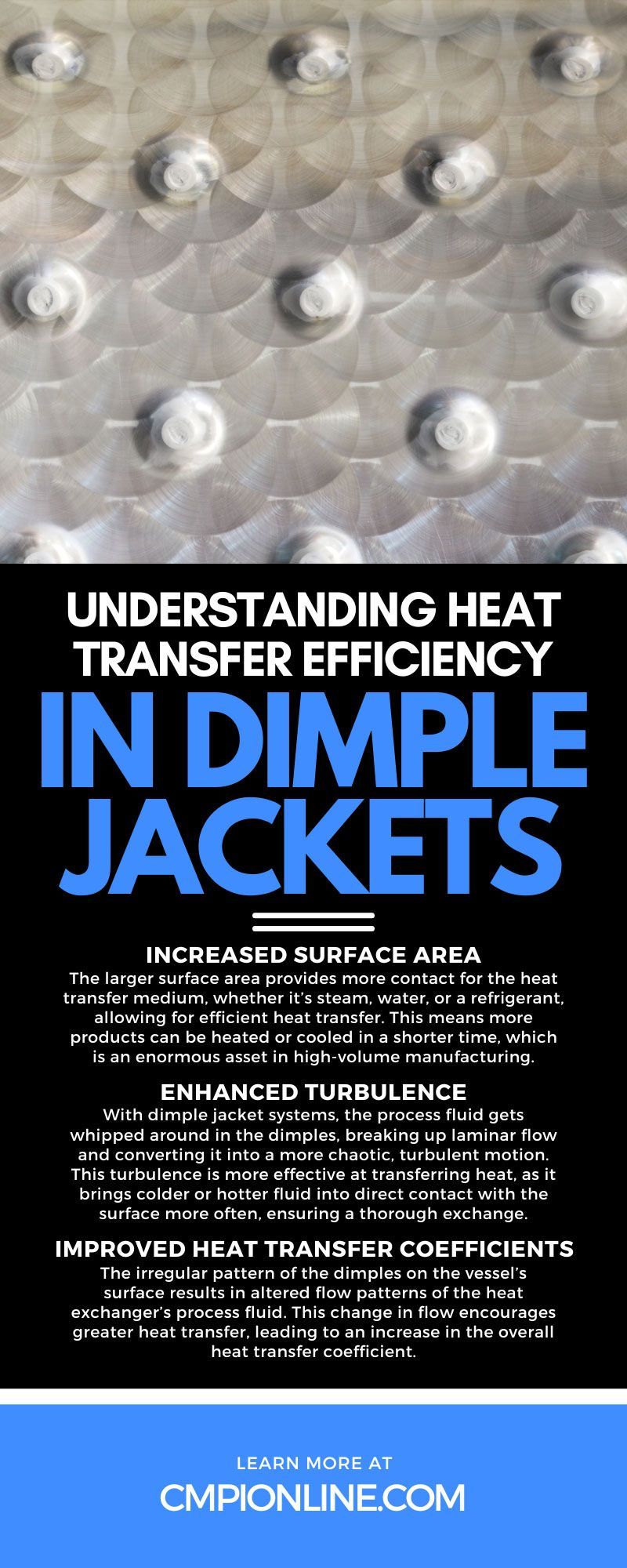